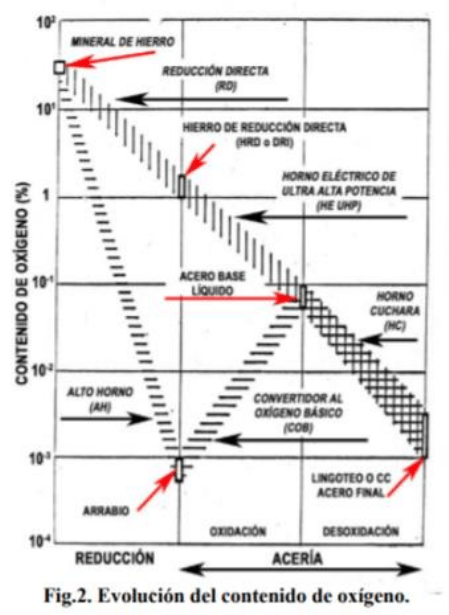
3
Entre los elementos más perjudiciales para el acero están el S y el P, sus contenidos deben
ser lo más bajo posible. Cuando el mineral se procesa mediante módulos de reducción
directa, se reduce el hierro pero la ganga pasa toda al siguiente proceso en acería, puesto
que no hay fusión, por lo cual el mineral
empleado en este caso debe ser de una
mejor calidad que el destinado al alto
horno.
1. Proceso alto horno: se tiene el
material de hierro dentro del horno, se llega
al punto de fundición (que no siempre es
homogéneo, depende de la composición
química del material). Se produce la
reducción del oxígeno presente dentro del
mineral de hierro. Luego de obtener el
arrabio, entra en el proceso del convertidor
al oxígeno (inyecto oxígeno para eliminar
carbono, calcio, manganeso), llegando al
punto denominado ACERO BASE.
2. Reducción directa: no se funde el
material, se levanta la temperatura hasta
unos 200° de mineral de hierro, se le hace
circular determinados gases con carbono y
nitrógeno para eliminar el oxígeno, se
obtiene hierro de reducción directa o hierro esponja (estado sólido). Luego entra al
horno eléctrico de ultra alta potencia que consume mucha electricidad, llegando al
mismo punto de acero base líquido.
Luego ambos procesos después de llegar al punto de acero base, pasa a la metalurgia
de cuchara, le va a dar la composición química final para ese tipo de acero (%C, %Si,
%Cr), se realiza proceso de desoxidación liberando oxígeno. A partir de ahí elegimos
la colada continua para fabricar planchones, rieles, etc o las lingoteras que sirven para
procesos posteriores de fundición.
Mediante los dos procesos llegamos al ACERO BASE con bajo porcentaje de elementos
aleantes, aunque yo necesito la incorporación de nuevos elementos aleantes para que
me sirvan para la producción de determinados productos pasa a otro horno que se
llama metalurgia de cuchara, donde le vamos a incorporar nuevos elementos y vamos a
producir un acero, ese acero líquido ya listo para colar se vuelca en moldes o en la
colada continua
Luego de obtener acero base este pasa a un horno cuchara, por ultimo un lingoteo (que
es similar a lo que pasaba con el proceso del aluminio) o colada continua.